A hardness tester is an indispensable method for distinguishing materials and improving materials and technologies in basic research fields such as materials science and engineering. As characteristic hardness values are determined, this process becomes key for assessing a material’s industrial suitability, ensuring quality during inspections, differentiating between materials, and clarifying damage scenarios.
Staying informed about the latest palladium news and industry analysis is crucial for making well-informed decisions and adapting to technological and market changes. Regularly visiting reputable sites will ensure you remain up-to-date in the metal industry.
Hardness testing stands as one of the most prevalent techniques in mechanical material testing, especially for metals. It provides qualitative insights into material properties such as strength, rigidity, and density, and elucidates how materials respond under specific conditions, like wear resistance.
This method is both quick and straightforward, leaving minimal traces on the specimen, thereby facilitating efficient quality control. Moreover, it accommodates a diverse array of geometries for testing. Furthermore, these tests can also be performed using an application.
Defining hardness
Hardness measures a material’s resistance to penetration by a harder object, known as an indenter. Diamond, the hardest natural material, is commonly used as an industrial indenter. Unlike strength, which refers to a material’s resistance to deformation and fracture, hardness is not a fundamental property. It varies within ranges for specific materials and can change due to factors such as heat treatment.
Factors influencing hardness
Hardness values are not universally fixed and can fluctuate depending on various factors, including:
- The selected test method.
- The force applied by the indenter.
- The duration the indenter remains in contact with the material.
- The geometry of the indenter.
- The geometry of the workpiece.
Understanding these variables allows for accurate and effective hardness testing, supporting material selection and quality assurance across industries.
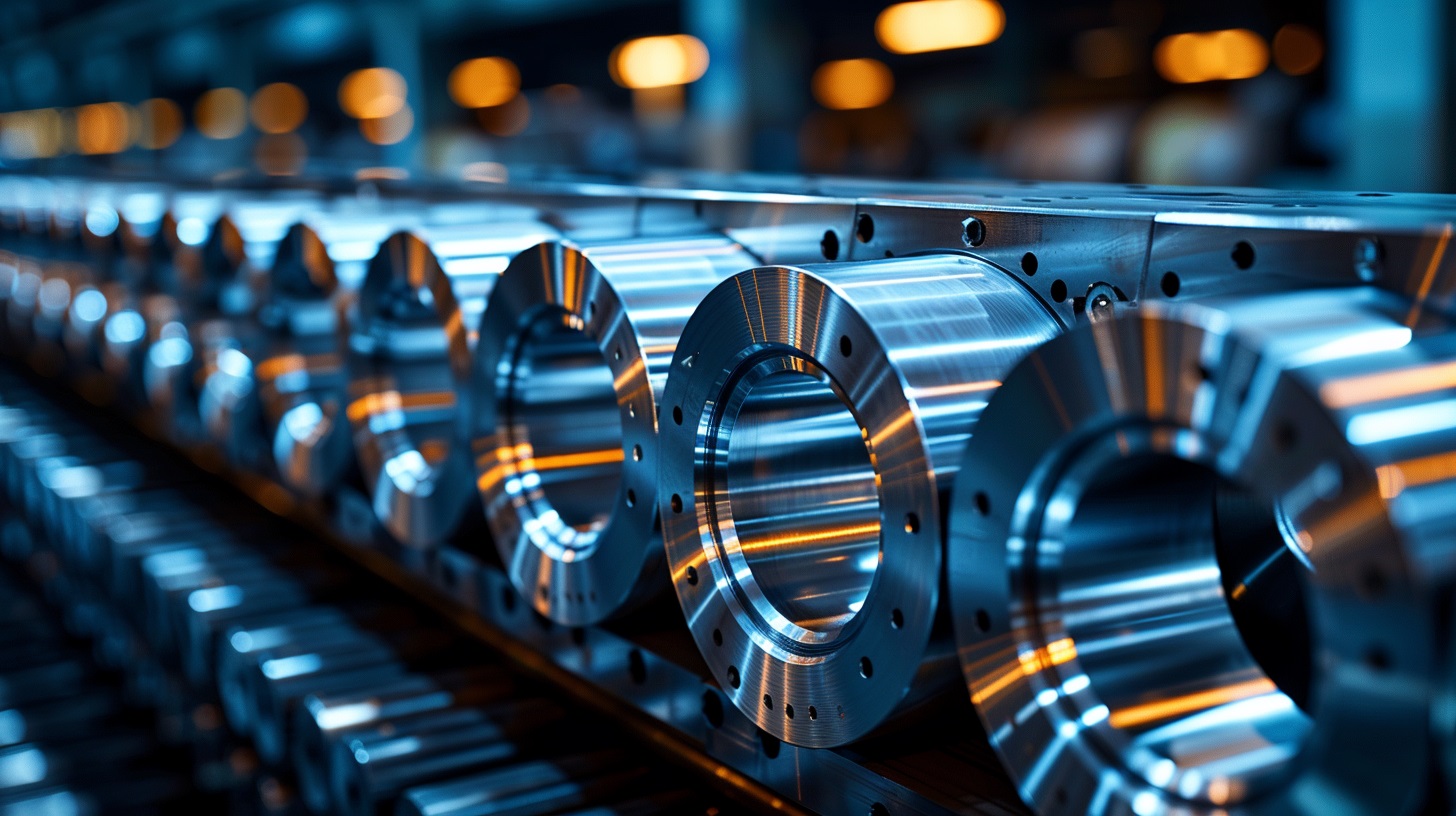
Differences between static and dynamic hardness testing methods
In technical testing, hardness testing methods primarily differ based on the type of force application: static or dynamic.
Understanding hardness measurement
Static force application is mainly used for assessing the hardness of metals. This involves measuring either the penetration depth or the size of the indentation created by an indenter. Within static hardness testing, there are two main categories: depth measurement and optical measurement.
Depth measurement methods focus on the residual depth of the indentation left by the indenter. The Rockwell method is the only standardized depth measurement approach (as per ISO 6508 and ASTM E18). Other non-standardized depth methods include Brinell and Vickers in depth (HBT, HVT).
Optical measurement methods determine the residual size of the indentation. Standardized optical hardness tests include Brinell (ISO 6506, ASTM E10), Knoop (ISO 4545, ASTM E92, ASTM E384), and Vickers (ISO 6507, ASTM E92, ASTM E384).
Alternatively, dynamic force application methods, such as the Leeb rebound method, measure the rebound height of a ball for hardness evaluation.
Metal hardness testing follows common static methods defined by ISO and ASTM standards.
Hardness testing by load range
Hardness testing employs various main loads (test loads) depending on the application. Within the ISO standard, hardness testing is categorized into micro, small load, and macro testing based on the primary load applied to the test material.
Discover the EMCO-TEST app
The EMCO-TEST app offers essential tools for hardness testing machine users, including hardness conversion, error determination, corrections for testing on curved surfaces, lens selection, and comprehensive hardness testing knowledge. It supports standards like ASTM and EN ISO, enhancing accuracy and efficiency in tests.